
They are going to want the work and they'll let me know what they can and cant do or what will make it more difficult or more expensive. I just call up a potential supplier and give them a rough draft and ask my questions.

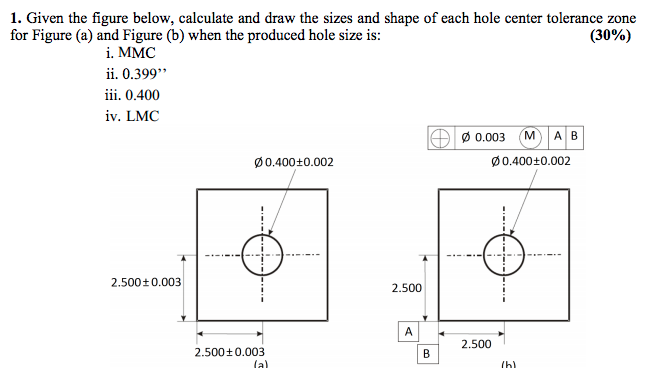
If I'm doing something I'm not used to like wire EDM. However, if you can make it +-.040 and its fine do that, it will be faster, cheaper, and cause less issues.
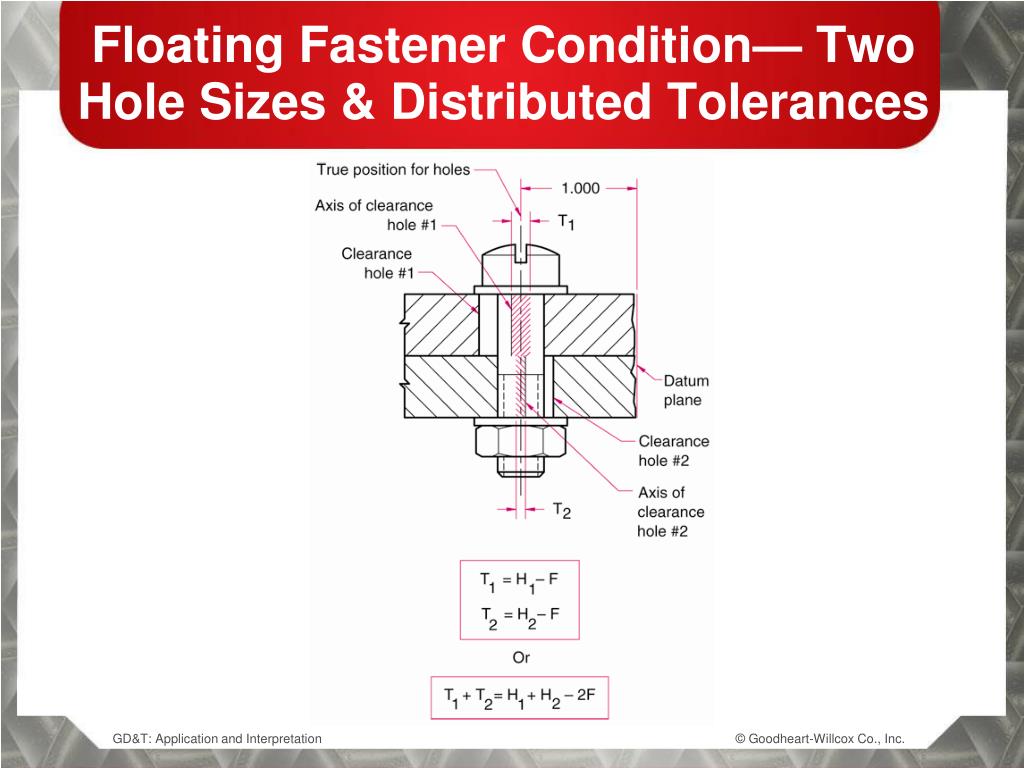
This might just mean more time between setups, might mean extra scrap parts, might mean more expensive, might mean its done a better/newer/more axis/more expensive mill. But if its between features between multiple setups on the mill, its going to be harder. Its just practice and experience.005 on a mill hole to hole isnt too bad. Do tolerance stack ups and see if two worst case example parts will still fit. Look up what is tight, normal, loose for a given process. Look at other peoples drawings and tolerances. Get feedback from the people that quote and make your stuff. Your problem isn't "how do I translate a machine's accuracy into GD&T" - what you need to figure out is how to calculate the accuracy your part requires, and dimension that instead. GD&T is all about how bad a part can suck before it won't work. Without redesigning or modifying a model in any way, I got the cost of their electronics enclosure from costing a little over $300 to $12 by doing a simple GD&T analysis, and redlining 4 drawings and they still worked exactly the same as before. The example I always use, for the proper application of GD&T: I was hired into a company to help them bring their manufacturing costs down, and standardize their build and testing procedures for the 4 things that they made. I've designed sheet metal parts that had no dimensions on the drawing at all and just a standard note about "0.030" tolerance on all undimensioned features" and we made thousands of them, dirt-freaking-cheap. I've designed parts where I have a pair of surfaces that are lapped to within 0.0001" profile tolerance, for a very specific reason, and features located elsewhere on the part with 0.030" positional tolerances, because I don't really give a crap where they are and a half-drunk machinist can eyeball a. It's about specify how bad it can suck and you'll still pay for it.įor reference.

GD&T is not about specifying how perfect your part CAN be. Make tolerances as loose as you can, but that will still make a part that works. 005" tolerance, that's going to be an expensive part, really fast. 005" don't just use that as your default tolerance. It doesn't matter if you can manufacture something, if that something doesn't work.Įven though you can assume a machine will hit. Once you know what you need, then you figure out if you can make it. You don't dimension for a manufacturing method.
